冲击伴随动力传动全过程,尤其在设备起动过程,这是造成系统设备损坏主要原因之一。在动力系统采用各种柔性联轴器是减缓冲击常用手段。长期以来,联轴器的耗能不被重视,如何选用不耗能的柔性联轴器,既能柔性起动负载,运行过程又不耗能!
常用柔性联轴器方案见下表:
表1 常用柔性联轴器方案负载起动、运行耗能、过载机械断开保护、运行柔性、对中要求、隔振功能对比
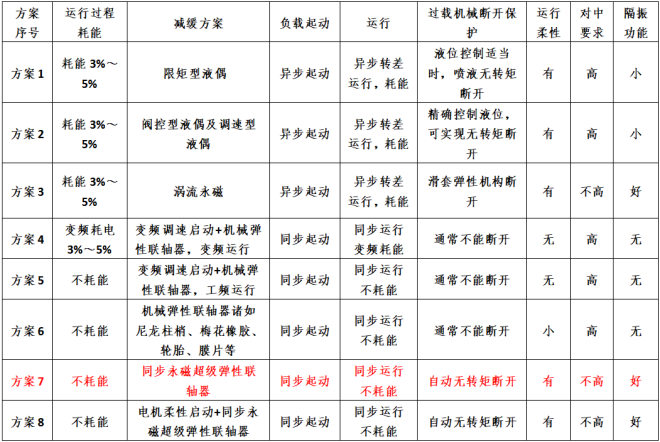
表2 常用柔性联轴器方案的优点、缺点及其最适合场合
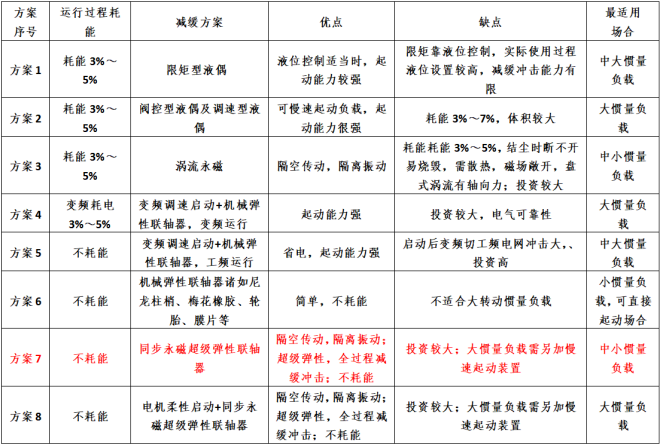
从上表可以看出,异步起动转差运行类的柔性联轴器存在3%~7%耗能,在选型过程应尽量避免。柔性联轴器尽量选用上表后四种减缓冲击方案!同步运行类联轴器运行过程不耗能,是首选的减缓冲击方案。传统的机械类同步联轴器,由于其弹性减缓冲击能力有限,单独使用通常仅适用小惯量负载;同步永磁超级弹性联轴器由于其超级弹性变形(7.5~15度,最大90度),减缓冲击能力显著增强,使同步联轴器成功应用到中等惯量负载,为节能传动提供了一全新产品,也是唯一入选国家发改委《低碳目录》的联轴器。
同步永磁超级弹性联轴器的工作原理
利用稀土永磁纯物理吸力,同步传递转矩。
同步永磁超级弹性联轴器节能贡献
在用同步永磁超级弹性联轴器已近万台,电机总功率近80万kW,以原使用液力耦合器(涡流永磁耦合器)对比估算,同步永磁超级弹性联轴器传动效率 99.9%,不发热,液力耦合器由于其原理特性,传动效率约93%~ 97%,液力耦合器按5%耗能计,即同步永磁超级弹性联轴器平均节电5%:
在用同步永磁超级弹性联轴器每年总节电量:
80万kW*7000 小时/年*0.6元/度*5%=1.68亿元/年
同步永磁超级弹性联轴器典型应用场合
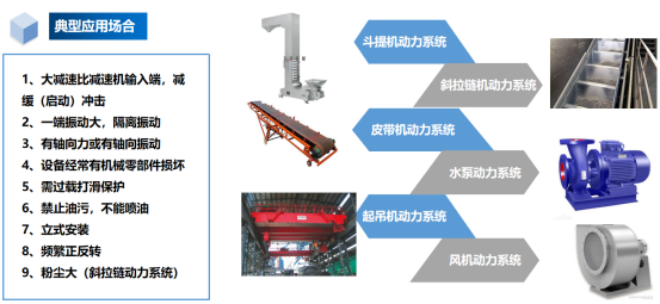
同步永磁超级弹性联轴器典型应用案例
钢铁行业:
防冲击典型案例--攀枝花钢钒有限公司钢包车动力系统
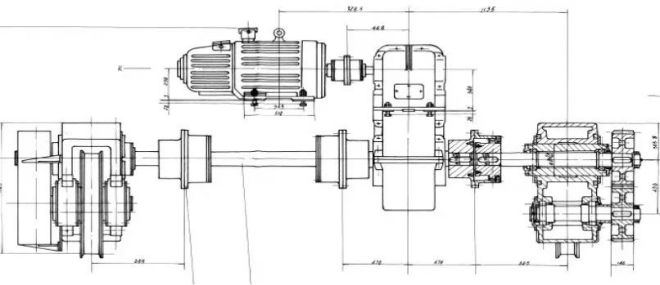
钢包车为160吨,加之频繁启动、刹车、颠簸,刚性冲击造成了低速端GL10大转矩齿轮联轴器容易损坏、寿命较短。
改造情况:通过更换了平时不坏的高速端小转矩齿轮联轴器(GL4)为同步永磁弹性联轴器,对低速端GL10大转矩齿轮联轴器未采取任何措施,解决了平时低速端GL10大转矩齿轮联轴器经常损坏问题。
使用结论:使用同步永磁弹性联轴器,将整个传动链都变成了柔性传动。这效果是涡流永磁及其它联轴器不能做到的。
防止轴套磨损典型案例—吉林建龙钢铁水泵动力系统
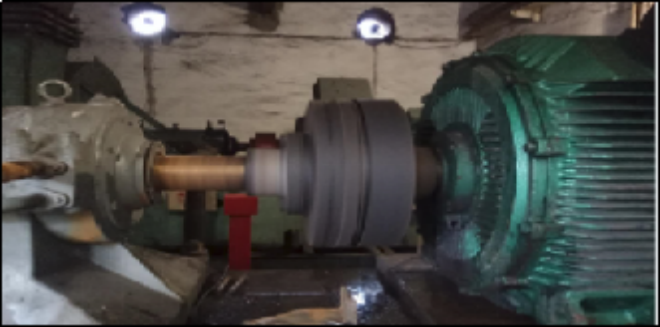
用户反馈:
改造前,由于振动轴瓦寿命不到一年,改造后大幅隔离了振动,提高了传动系统的柔度,有效防止了轴套磨损,运行至今状况良好。
兴澄特钢皮带机动力系统——取代限矩型液偶,节电5%
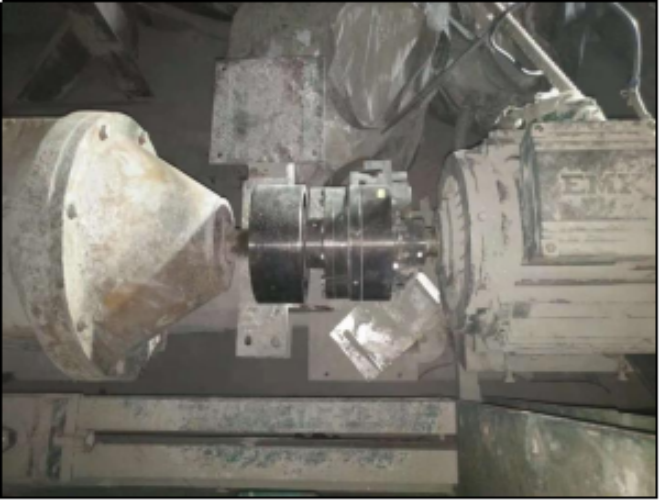
用户反馈:
使用同步永磁弹性联轴器替换原液耦后,将整个传动链都变成了柔性传动,隔振降噪,无液压油消耗。
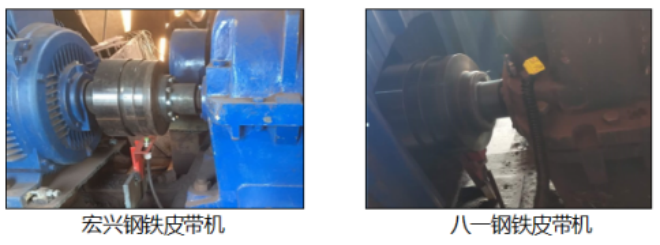
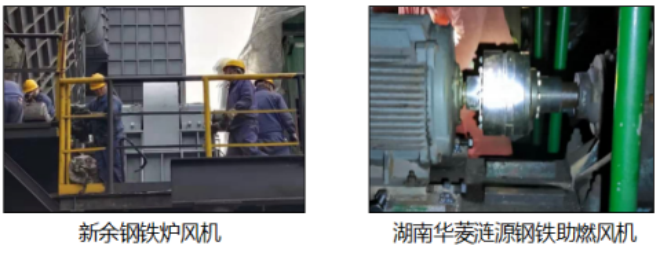
水泥行业:
皮带机——取代限矩型液偶,节电5%
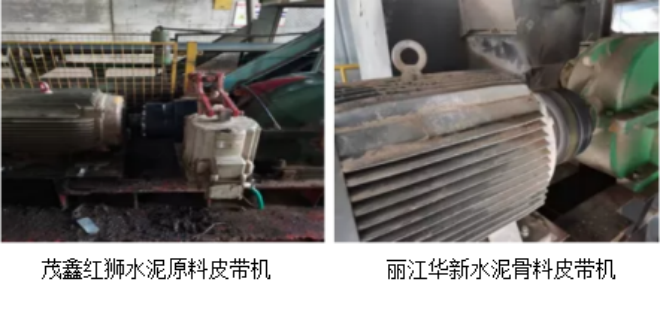
刮板机——取代限矩型液偶,节电5%
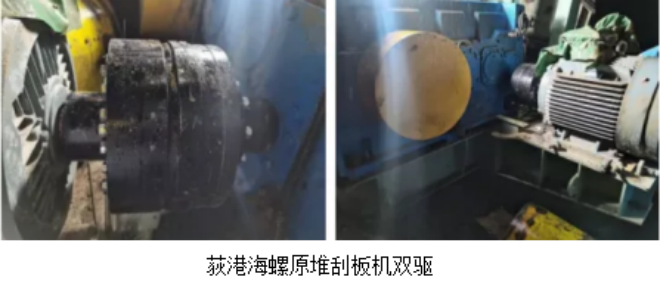
辊压机——取代限矩型液偶,节电5%
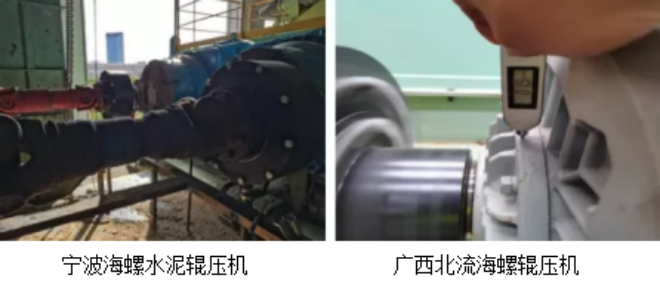
斗提机——取代限矩型液偶,节电5%
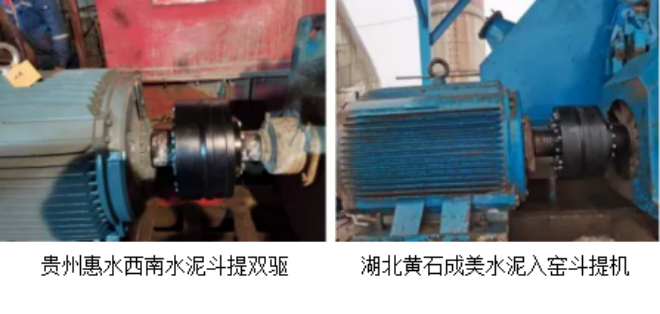
电力行业:
防正反转典型案例--国能投谏壁发电有限公司斗轮机动力系统
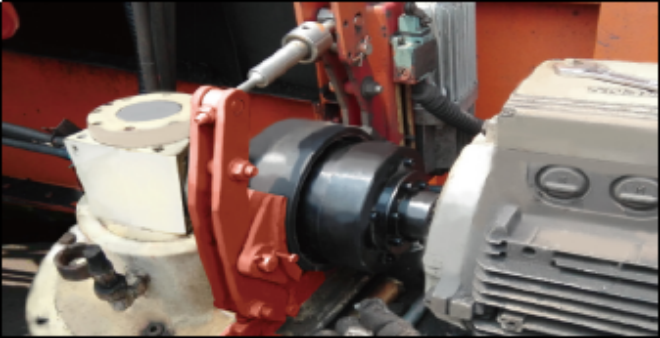
应用情况:
在频繁正反转斗轮机大臂回转电机上使用同步永磁弹性联轴器,不但减缓了振动;而且由于给整个传动系统提供了的弹性柔性,打破了进口设备正反转转换前必须先刹停再转换的运行模式,彻底弃用辅助刹车系统,使直接正反转转换也不损坏输出低速端齿轮成为现实,运行至今状况良好。这是任何其它类(含涡流永磁)不可做到的功能。
替代液偶典型案例--中电投大别山发电有限责任公司皮带机动力系统
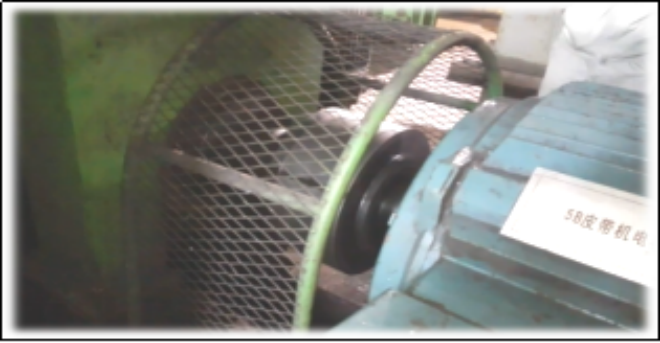
用户反馈:
采用江苏磁谷同步永磁弹性联轴器代替液偶,使用后柔性启动效果非常好,对整个传动系统都有很好的保护,大幅度降低了振动且使用效率高有节电空间,系统出现故障能自动打滑保护。
使用效果:
有效减缓皮带机起动时冲击;隔振降噪;节电约5%;零消耗;零维护。
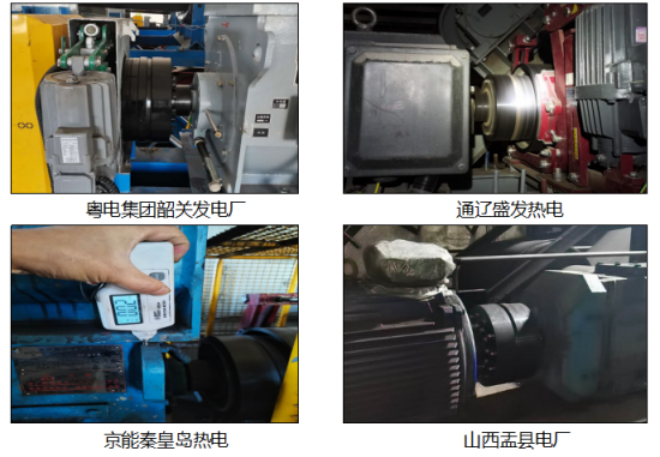
化工行业
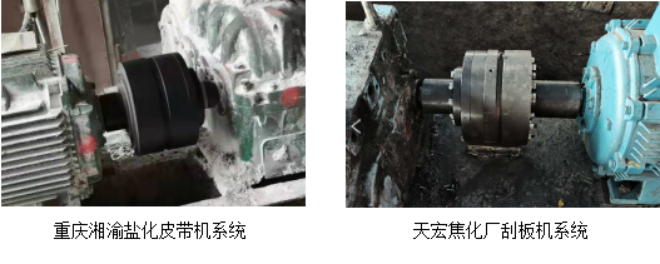
煤炭行业
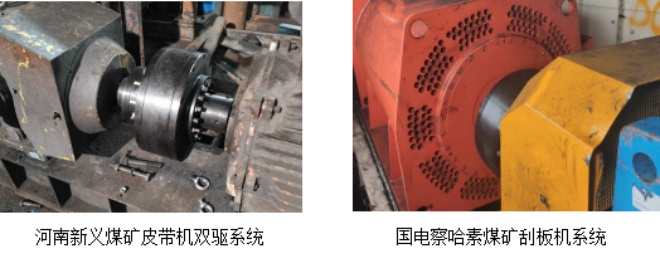
多个实际应用案例表明,江苏磁谷同步永磁弹性联轴器为新一代永磁耦合器,自身使用寿命20年,采用磁悬浮非接触式磁场传动,隔振降噪,拥有超级弹性位移,弹性位移(角)达7.5~15度(最高可达90度),能有效缓解冲击载荷,将整个传动链都变成柔性传动,提升过载保护力,保护轴系设备以及整个传动链,延长电机和其他设备的使用年限,提高整个传动链所有设备寿命3~5年,在全使用寿命(大于15年)内无维护,提高生产可靠性,降低因传动问题导致停产的风险,大大提高生产效率机场可靠性,节约生产成本;此外全封闭不漏磁,更安全环保,适宜粉尘高温等恶劣环境;传递效率接近100%,无滑差、不丢转、无散热片、传递效率更高,相比转差类联轴器节能约5%;筒式结构、结构简单、轻便,环绕轴传递力矩、无轴向力、不会因永磁盘和导体盘相吸受负载波动影响而造成轴向窜动;安装方便,允许毫米级对中误差。
咨询电话:徐总 13906104105(微信同号)
江苏磁谷科技股份有限公司